Risk Management Process
You must manage risks to health and safety using the HSW Act hierarchy of controls.
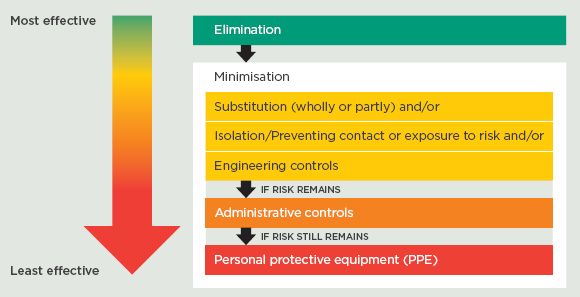
Hierarchy of controls (courtesy of Worksafe NZ)
Explanation and some examples of the different levels of controls
- Elimination is removing the source of harm
- getting rid of unwanted chemicals
- using another pest control method not involving agrichemicals
- Substitution is using lower risk alternative
- using less hazardous products or formulations.
- Isolation is separating the person from the risk
- applying insecticides from inside an enclosed tractor cab.
- Engineering controls use mechanical devices or processes
- ventilation systems
- robotic spraying.
- Administrative controls are procedures or rules for workers to follow
- prohibiting eating and drinking near hazardous substances
- only using a designated mixing site
- respirator filter replacement policies.
- PPE is used to reduce exposure to any remaining risk. (Note that PPE is the last, not the first, level of risk management.)
- gloves
- respirators
- overalls
- eye protection
- etc.
Some controls are required by law. Others will be determined by you as part of your risk management planning.
Some legal controls are based on the individual product – this information is on the label. Other controls are based on the total quantity and type of products stored. These requirements are covered in the chapters on Storage and Emergency Planning in this manual.
You must review your hazardous substances controls after:
- any significant changes to the product
- any emergency event involving agrichemicals, or
- at least every five years.
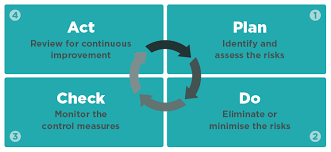
Image courtesy of WorkSafe
 |
More information can be found in WorkSafe’s Quick Guide to Hazardous substance risk management. |